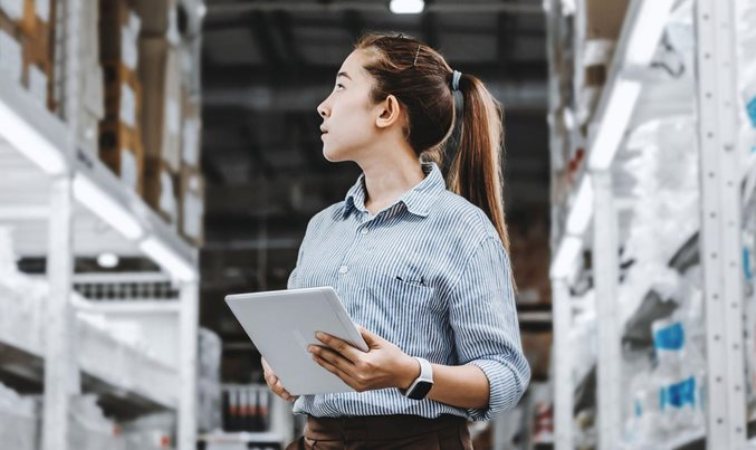
Corona virus and technology supply chains: How to restart and rebuild
For the technology industry, the effects of the corona virus (SARS-CoV-2), which causes COVID-19 disease, started to take hold in January when China a critical link in the global technology chain began reporting more cases. And while the country’s early lockdowns and quarantines are slowly beginning to lift, the pandemic’s international expansion is leading to new restrictions across the globe that are weighing on business activity. Consequently, the technology supply chain now faces a new set of challenges.
China itself poses several operational questions. Over the past few weeks, major progress in reducing labor constraints in China occurred. We estimate that by March 24, 2020, around 75 percent of the country’s workforce had returned to work. That is a major improvement over the situation in February 2020, when less than 20 percent of workers were back on the job. But many workers are new recruits who require training, which will likely take several more weeks. And Wuhan the major manufacturing center where the outbreak began remains far behind, with just around 24 percent of labor having returned to work.
Optimize limited production capacity
After obtaining the adjusted demand figures, manufacturing departments should allocate capacity based on an integrated, quantitative production-prioritization matrix. Here, it is necessary to strike a fine balance between customer needs and production efficiency, while also considering each customer’s strategic importance, related customer-service implications, component availability, and production efficiency.
Consider a manufacturer that is facing a dozen orders, each for more than 10,000 units across three major product types. Because of supply shortages, realistic productive capacity is only about 50,000 units less than half of the cumulative orders.
Commercial considerations matter most. One important customer is experiencing a stock out so severe that it has threatened to stop offering the product if it isn’t replenished. That order goes to the front of the queue: it’s for one of the manufacturer’s core products, and the manufacturer can’t afford to lose the relationship. Manufacturability then enters the equation. The priority order is produced, and the remaining available capacity goes to the next three orders for the same product family, making them easier to produce: one order for an overseas customer experiencing a stock out, another that was bundled with the top-priority order, and a third for a no priority customer whose order could be filled by the same manufacturing run.
The remaining orders above the daily capacity fall into backlog for next-day production, unless pushed again by new prioritization from customers or changes in availability of parts illustrating an urgent need for frequent (ideally daily) sales and operations planning.
Recommended actions over the medium term
As time passes, organizations will be able to move out of the current crisis mode. In the medium term a period of the next two to four months a further set of actions should be taken. They should include the conversion of the nerve center into a midterm risk-management process, with business continuity tested on a regular basis.
Convert daily firefighting into reliable risk management
While companies use temporary processes to conduct short-term risk management, they must gradually streamline, over a period of two to four months, this daily firefighting into a more formalized risk-management process. They can use the knowledge and lessons learned from their short-term actions to form the basis for building a more resilient supply chain. This should include building a risk-management team in addition to the temporary taskforce managing catastrophic events to assess supply-chain risk, with a clear information cascade. There should also be regular interfacing with other functions, including sales and marketing, finance, HR, R&D, and IT, to ensure and encourage a high awareness of the importance and implications of proper supply-chain risk management.
Additionally, the team should communicate frequently with other stakeholders, such as policy makers, investors, and others, to ensure that they are aware of any changes that will affect them as early as possible. The team should also identify any relevant new tax and government incentives that could support the company, either directly or indirectly through impact on others in the supply chain.
Part of building a more robust supply-chain risk-management process will also include building structural flexibility. When possible, companies should implement a multisource approach for critical components, along with local supply-chain monitoring supported by local sourcing hubs.
McKinsey