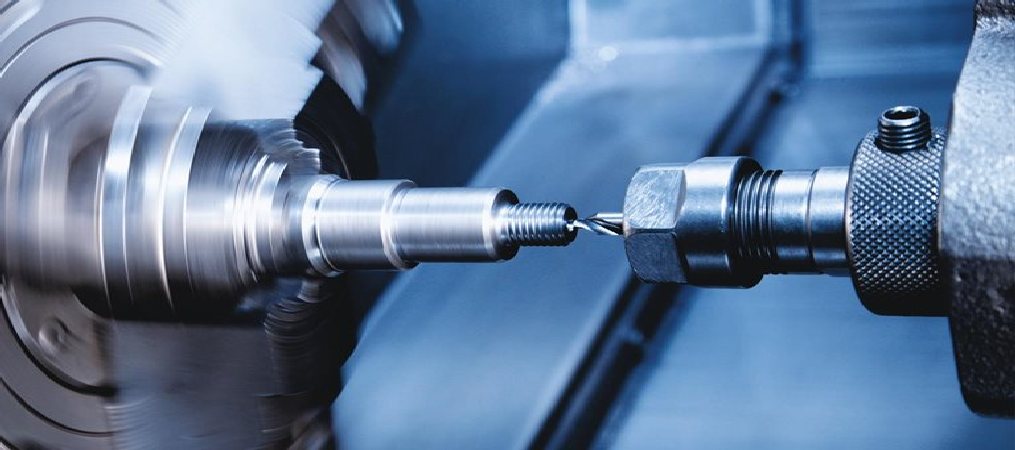
Coronavirus: Industrial IoT in challenging times
Industrial companies expected 2020 to bring economic pressure from ongoing trade disputes, the aftermath of Brexit, automotive-industry challenges, and slowing demand in China. But none anticipated that the COVID-19 pandemic would throw the global economy, and their own operations, into an unprecedented crisis. As the coronavirus continues to spread, governments, healthcare authorities, and business leaders are focused on preserving lives and containing the pandemic. In parallel, they want to lessen the humanitarian toll by protecting the livelihoods of millions of workers who are now furloughed, unemployed, or in danger of losing their jobs.
Within industrials, shocks to both supply and demand have significantly decreased production volumes or stopped operations. For instance, all major automotive OEMs in Europe have shut down their production networks, resulting in the breakdown of entire value chains. Where business has continued, physical-distancing measures are dramatically altering operations, employee responsibilities, and staffing.
To navigate the current crisis and reach the next normal that will emerge after the pandemic abates, companies must embark on a journey with three horizons, each of which involves different questions:
How can we ensure business continuity now?
- Return and resilience.
How can we return to business and increase our flexibility to thrive in the “new normal”?
- Reimagination and reform.
How can we improve our business over the long term, in a world changed by the pandemic, and emerge even stronger?
Industrial IoT (IIoT), a major element of Industry 4.0, can help companies as they proceed on this journey. It has demonstrated its value on many occasions over the past few years, but some skeptics still doubt its worth and elected not to make bold investments in this area. What’s more, few business leaders view IIoT as a critical improvement lever in times of crisis, especially if their organizations have not previously explored it.
Lowering costs in the short term
As the crisis unfolds, industrials can benefit from short-term cost reductions, and several IIoT-enabled tools can help in this respect.
Digital performance management.
IIoT-based software solutions can provide a real-time dashboard of key performance indicators to support shop-floor performance dialogs, increasing transparency. These tools also allow the tracking of improvement actions and send alerts to operators via mobile devices. The software evaluates machine data, such as information on overall equipment effectiveness, part production, and quality through IIoT connectivity. Improved performance management can help companies boost labor productivity by 20 to 40 percent.3
Remote assistance.
In addition to improving employee safety, experience suggests that remote assistance and maintenance tools can yield a 10 to 40 percent reduction in field-service costs, especially travel, by reducing the need for in-person visits. The gains may be particularly high at machinery OEMs with a large installed base.
Connectivity and cyber security
Strong connectivity and cybersecurity enable better visibility across the supply chain, allowing industrials to respond more rapidly to disruptions. The time required to improve connectivity and cybersecurity will vary, depending largely on a company’s operational setup, including the number of machines and software solutions in place.
Large-scale connectivity rollouts.
Many companies have a pressing need to provide employees with remote access and control of various machines. Since many machines are now experiencing higher-than-usual downtime, companies may be able to install connectivity kits on them more easily. To accelerate the rollout, workers could install a connectivity box each time they perform routine maintenance services. Every machine that is connected to the internet will help industrials, since it becomes available for remote monitoring, data collection, and other services.
Cybersecurity.
As companies increasingly digitize their manufacturing operations, cybersecurity becomes more important. As with large-scale connectivity, companies can more easily improve cybersecurity at all levels when asset downtime is high or operations are shut down, since applying fixes will not create major disruptions. Companies can undertake some simple cybersecurity measures, such as critical software updates and firmware updates of hardware, fairly quickly. These small steps help to minimize overall cybersecurity risks.
Mid-term cost improvement and flexibility
There are several IIoT use cases that can help industrial companies adjust to the next normal after the crisis by reducing their break-even point and creating a more flexible cost basis.
IIoT-enabled asset optimization.
This use case involves using advanced analytics to identify the root causes and countermeasures related to the three drivers of overall equipment effectiveness (OEE): availability, performance, and quality. For instance, an aerospace supplier had a low OEE when producing an important airplane component. It then used IIoT solutions to monitor and detect certain problems, such as tool wear and missing materials. Based on this sensor information, the company was able to optimize job sequences in a central control room. With these improvements, the company achieved 80 percent OEE. IIoT tools may also help companies discover previously unknown problems within the supply chain. While impact may vary drastically across settings, companies may improve OEE by as much as five percentage points—for example in low-volume, high complexity discrete manufacturing settings.
Real-time procurement transparency.
IIoT tools can help companies optimize procurement by using real-time information on inventory levels and production capacity to determine what quantities must be ordered and assist with rapid contract renegotiations. This feature is especially relevant during the current crisis because commodity prices have decreased significantly. Take oil and copper, both of which have decreased in price by about 20 to 25 percent. Optimizing vendor allocations and improving negotiation strategies typically deliver a 2 to 5 percent reduction in raw-material costs. Given current events, these savings will likely be higher now.
McKinsey